In today’s fast-paced and evolving workplaces, ensuring the well-being of employees is not just a moral obligation but also a critical component of a successful business. Occupational Safety And Health (OSH) is a multidisciplinary field dedicated to safeguarding workers' physical, mental, and social well-being across various industries. This guide delves into OSH, its importance, key components, and strategies for implementing an effective OSH program.
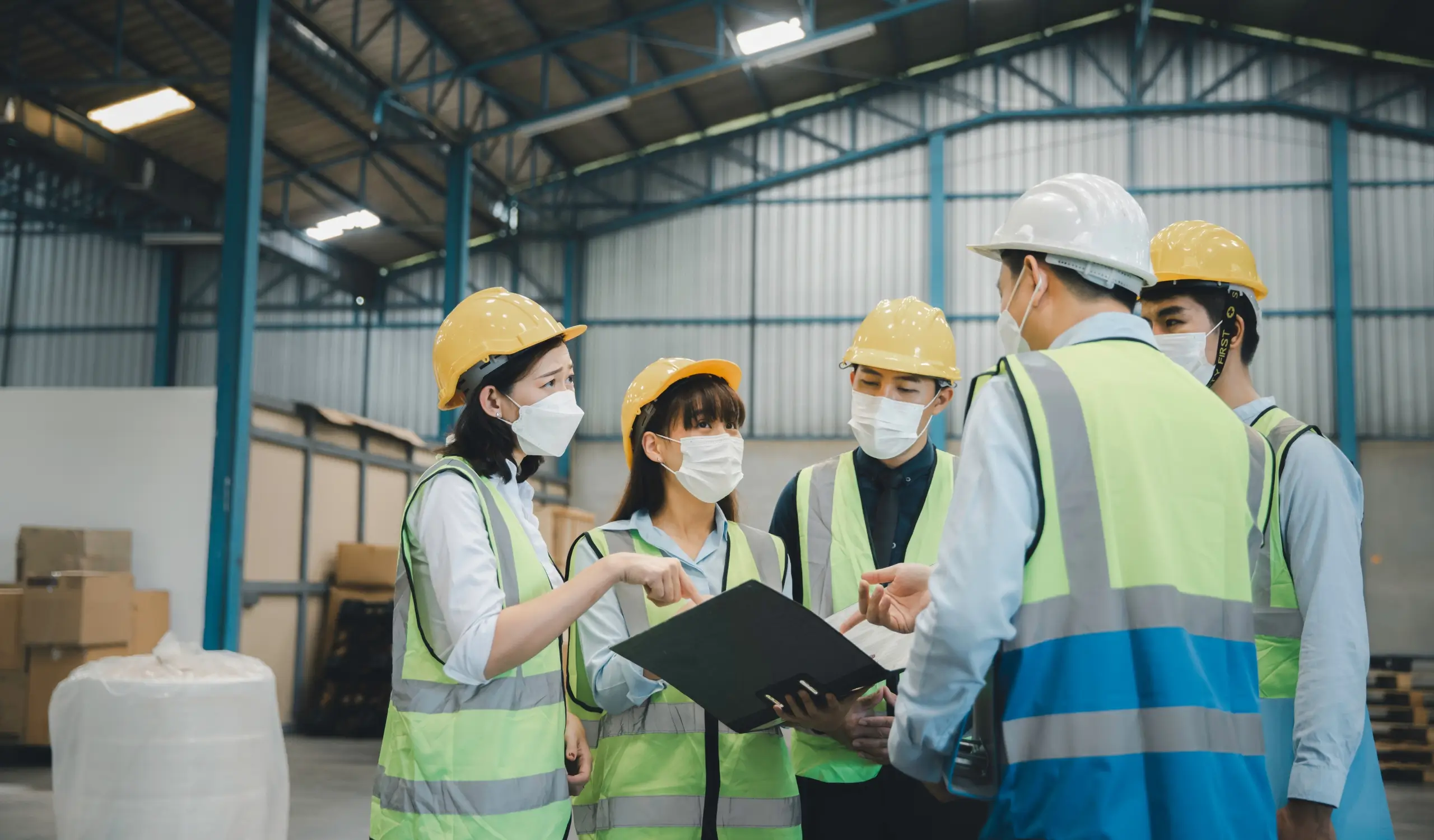
What is Occupational Safety And Health (OSH)?
Occupational Safety And Health refers to the policies, procedures, and practices designed to protect employees from workplace hazards. It encompasses a wide range of measures to prevent accidents, injuries, and illnesses while promoting a healthy work environment. OSH ensures compliance with legal standards and fosters a culture of safety and productivity.
Why is OSH Important?
- Protecting Workers’ Health: OSH programs focus on minimizing workplace hazards that can cause injuries or illnesses, ensuring employees return home safe and sound.
- Boosting Productivity: A safe and healthy workplace fosters employee morale, reduces absenteeism, and enhances overall productivity.
- Legal Compliance: Adhering to OSH regulations helps organizations avoid penalties, lawsuits, and reputational damage.
- Cost Savings: Preventing workplace accidents reduces expenses related to medical bills, compensation claims, and equipment damage.
- Reputation Management: Companies prioritizing OSH gain trust and credibility among employees, stakeholders, and customers.
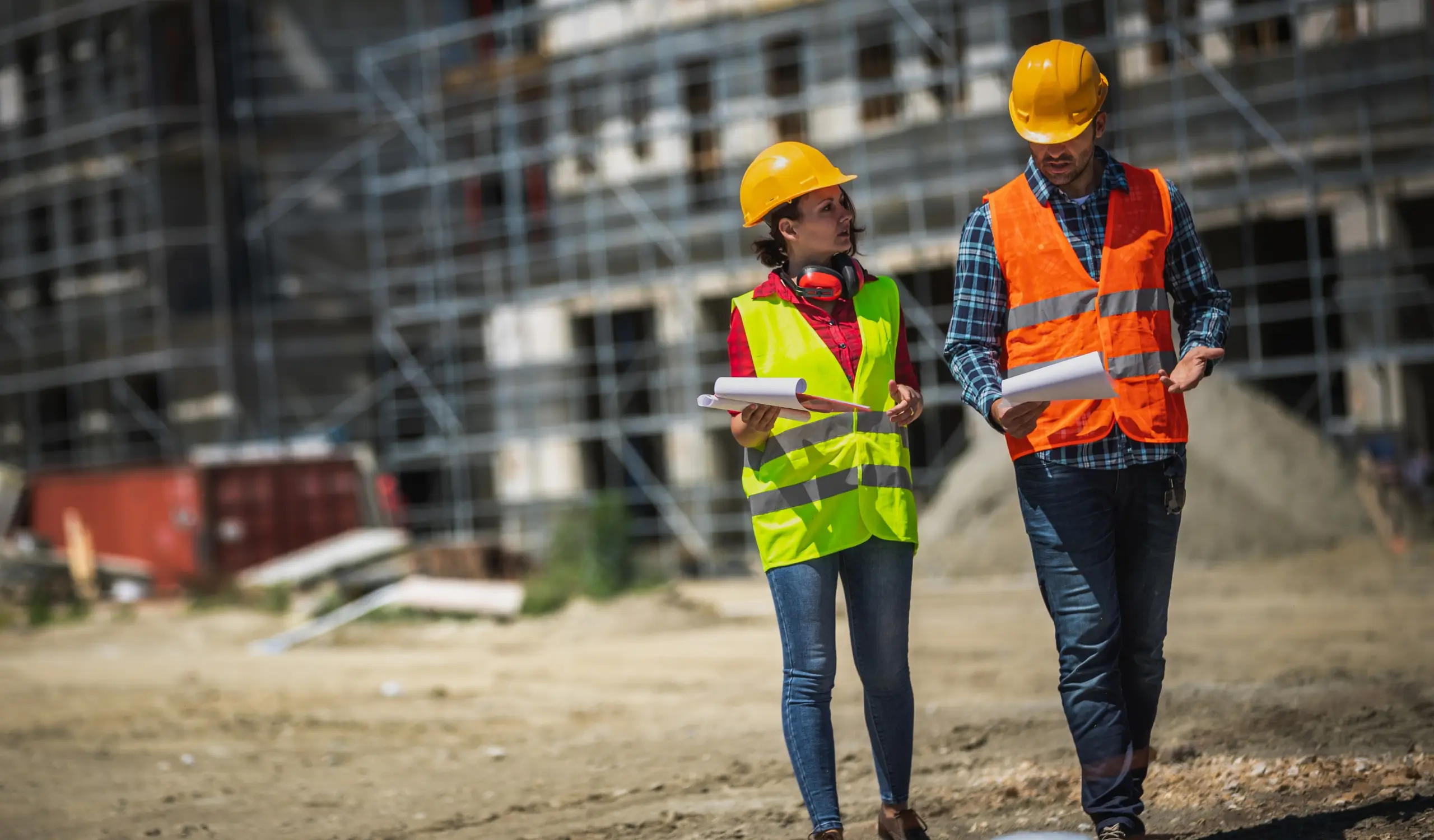
Key Components of an Effective OSH Program
Occupational Safety And Health (OSH) programs are essential for ensuring workplace safety and minimizing risks. Let's explain each component of an effective OSH program:
1. Hazard Identification and Risk Assessment
The cornerstone of any OSH program is regularly identifying potential hazards and assessing associated risks. This proactive approach ensures that potential dangers are mitigated before they lead to accidents or injuries.
Types of Hazards:
- Physical Hazards: These include unsafe conditions like machinery without guards, slippery floors, or excessive noise.
- Chemical Hazards: Exposure to harmful substances such as cleaning agents, fumes, or industrial chemicals.
- Biological Hazards: Risks from bacteria, viruses, or other pathogens, particularly in healthcare and laboratory settings.
- Ergonomic Hazards: Risks from repetitive motions, improper workstation setups, or heavy lifting.
Steps in Hazard Identification and Risk Assessment:
- Conduct workplace inspections to identify existing and potential hazards.
- Analyze tasks and work processes for risks.
- Assess the likelihood and severity of harm from identified hazards.
- Implement controls to eliminate or reduce risks, using methods like engineering controls, administrative actions, or personal protective equipment (PPE).
2. Safety Policies and Procedures
Establishing clear and comprehensive safety policies and procedures helps create a structured framework for maintaining workplace safety.
Key Elements:
- Safety Manual: A document outlining the organization’s safety objectives, policies, and detailed procedures for various scenarios.
- Standard Operating Procedures (SOPs): Step-by-step instructions for performing tasks safely.
- Roles and Responsibilities: Clear definition of duties for management, supervisors, and employees in upholding safety.
Benefits:
- Employees understand expectations and the importance of following safety practices.
- Consistency in enforcing safety protocols across all departments.
- Streamlined response during emergencies or incidents.
3. Training and Education
Ongoing training is vital to ensure that employees are knowledgeable about workplace hazards and equipped to respond to emergencies effectively.
Types of Training:
- Orientation Training: Introduces new hires to safety policies and workplace-specific hazards.
- Task-Specific Training: Focused on hazards and safe practices related to specific roles or equipment.
- Refresher Courses: Regular updates on safety practices to reinforce knowledge and address new risks.
Benefits of Training:
- Employees are better equipped to recognize and avoid hazards.
- Reduces accidents caused by lack of awareness or improper practices.
- Fosters a culture of safety, where employees actively participate in maintaining a safe environment.
4. Emergency Preparedness
An effective OSH program includes comprehensive planning for emergencies to minimize harm and chaos when unexpected events occur.
Key Elements:
- Evacuation Procedures: Clear guidelines on evacuation routes, assembly points, and roles during emergencies.
- First Aid Training: Employees trained in basic first aid can provide immediate assistance, reducing the severity of injuries.
- Emergency Kits: Stocked with essential items like first aid supplies, flashlights, and communication tools.
Types of Emergencies to Prepare For:
- Fires
- Chemical spills
- Natural disasters (e.g., earthquakes, floods)
- Workplace violence or active shooter situations
Regular Drills: Conducting fire drills, spill containment exercises, and other practice scenarios ensures employees are familiar with protocols and can respond quickly under pressure.
5. Monitoring and Auditing
Continuous monitoring and regular audits help maintain high safety standards by identifying areas needing improvement and ensuring compliance with regulations.
Activities:
- Routine Inspections: Daily or weekly checks of equipment, tools, and work areas to identify hazards.
- Compliance Audits: Periodic reviews to ensure adherence to local, national, and industry-specific safety regulations.
- Incident Investigations: Analyzing accidents and near-misses to uncover root causes and prevent recurrence.
Benefits:
- Early detection of potential issues before they escalate.
- Evidence of compliance for regulatory bodies or insurers.
- A systematic approach to continuous improvement.
6. Employee Participation
Engaging employees in the development and implementation of OSH programs fosters a sense of ownership and accountability.
Ways to Encourage Participation:
- Safety Committees: Involve representatives from different departments to discuss and address safety concerns.
- Suggestion Systems: Allow employees to report hazards or propose improvements anonymously.
- Recognition Programs: Reward employees who demonstrate exemplary safety practices or suggest innovative safety solutions.
Benefits of Employee Involvement:
- Employees often have firsthand knowledge of workplace conditions and can provide practical insights into hazards.
- Increased compliance with safety measures when employees feel their input is valued.
- Promotes a collaborative safety culture where everyone is invested in each other’s well-being.
An effective OSH program integrates hazard identification, clear policies, robust training, preparedness for emergencies, regular monitoring, and active employee participation. By addressing these components, organizations can create a safer, more productive workplace where risks are minimized and employees thrive.
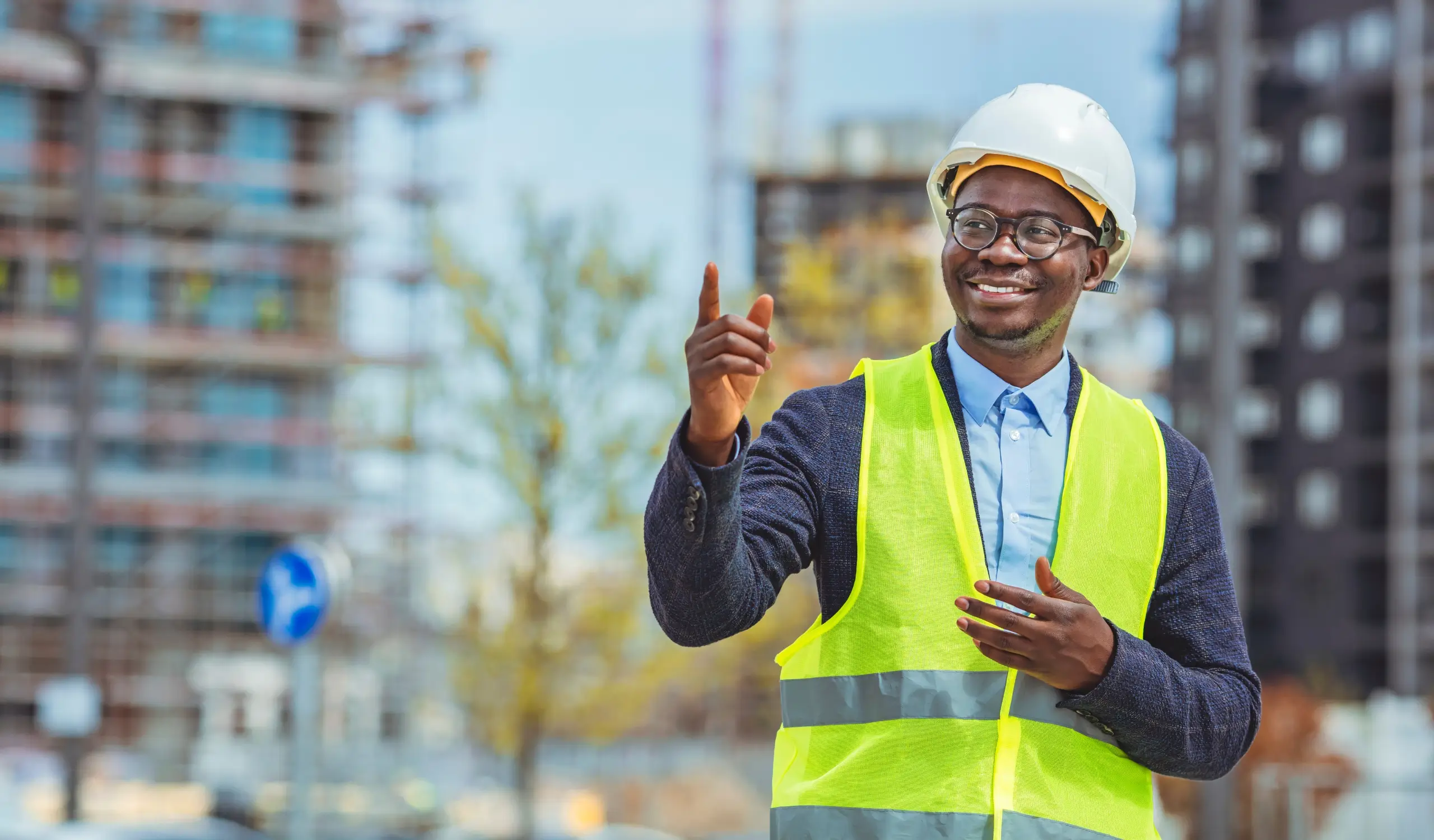
Common OSH Challenges and Solutions
Occupational Safety And Health (OSH) implementation often faces various challenges, from lack of awareness to resistance to change. Below is an exploration of common OSH challenges and practical solutions to overcome them:
1. Lack of Awareness and Training
Many workers and managers may be unaware of workplace hazards or the importance of safety procedures. Insufficient training can lead to unsafe practices, accidents, and non-compliance with regulations.
Solution:
- Comprehensive Training Programs: Implement tailored training sessions covering general safety protocols, job-specific hazards, and emergency response.
- Continuous Learning: Conduct regular refresher courses and updates on new safety regulations or procedures.
- Visual Aids and Signage: Use posters, labels, and safety signs to reinforce training and increase hazard awareness on-site.
2. Non-compliance with Safety Regulations
Failure to comply with safety standards can result from negligence, lack of understanding, or a focus on productivity over safety. This can lead to legal penalties, reputational damage, and workplace accidents.
Solution:
- Clear Safety Policies: Develop and communicate clear policies aligned with local and international regulations.
- Regular Audits: Conduct inspections and compliance audits to identify and correct non-conformities.
- Enforcement Measures: Institute penalties for repeated violations and recognize teams that demonstrate exemplary compliance.
3. Evolving Workplace Hazards
Workplaces are constantly changing due to new technologies, processes, or materials. These changes can introduce unfamiliar hazards that may go unaddressed.
Solution:
- Proactive Risk Assessments: Continuously evaluate new processes, machinery, or chemicals risks.
- Adaptable Policies: Regularly update safety protocols to reflect evolving workplace environments.
- Training on Emerging Risks: Ensure employees are educated on potential hazards related to new equipment or technologies.
4. Resistance to Change
Employees or management may resist implementing new OSH measures, viewing them as unnecessary, time-consuming, or disruptive to workflows.
Solution:
- Leadership Involvement: Gain commitment from management to model and champion safety initiatives.
- Employee Engagement: Involve employees in decision-making to foster a sense of ownership and acceptance of changes.
- Effective Communication: Clearly explain the benefits of OSH measures, emphasizing how they protect workers and improve productivity.
5. Limited Resources
Smaller organizations may face budgetary constraints, limiting their ability to invest in safety equipment, training, or personnel.
Solution:
- Prioritize High-Risk Areas: Focus resources on the most critical hazards to maximize impact.
- Leverage Technology: Use cost-effective safety tools like apps for incident reporting or online training platforms.
- Seek External Support: Apply for grants, partner with industry bodies, or consult external safety experts for guidance.
6. Ineffective Communication
A lack of clear communication can lead to misunderstandings about safety policies and inconsistent practices across the organization.
Solution:
- Simplified Messaging: Use plain language to ensure that all employees understand the policies, regardless of their education or experience level.
- Regular Updates: Share updates through multiple channels, such as emails, meetings, or noticeboards.
- Feedback Mechanisms: Encourage employees to voice concerns and ask questions about safety protocols.
7. Fatigue and Complacency
Employees accustomed to routine tasks may overlook hazards, leading to complacency. Fatigue can also impair judgment, increasing the likelihood of accidents.
Solution:
- Rotate Tasks: Implement job rotation to reduce monotony and help workers remain alert.
- Encourage Breaks: Schedule regular breaks, especially for physically demanding or repetitive tasks.
- Reinforce Awareness: Use toolbox talks and regular reminders to keep safety in employees’ minds.
8. Psychological Hazards
Stress, workplace bullying, and mental health issues can impact employees' overall safety and productivity.
Solution:
- Mental Health Support: Provide access to counseling services or employee assistance programs (EAPs).
- Foster a Positive Work Culture: Promote inclusivity and respect to reduce workplace conflicts.
- Monitor Workloads: Ensure workloads are manageable to prevent burnout and excessive stress.
9. Workplace Diversity
Cultural differences, language barriers, and varying levels of education can complicate the implementation of uniform safety practices.
Solution:
- Multilingual Resources: Provide training materials and safety instructions in multiple languages.
- Cultural Sensitivity Training: Educate staff on cultural differences to foster better understanding and cooperation.
- Universal Symbols: Use universally recognized safety symbols and visual aids.
10. Emergency Preparedness
Organizations may lack a structured plan to handle emergencies effectively, leading to confusion and increased risk during crises.
Solution:
- Comprehensive Plans: Develop detailed emergency response plans tailored to the organization’s risks.
- Regular Drills: Conduct fire drills, evacuation exercises, and other emergency simulations to test preparedness.
- Assign Roles: Designate responsibilities for key personnel, such as fire wardens or first responders.
Overcoming OSH challenges requires a proactive and collaborative approach. By addressing these common obstacles with practical solutions, organizations can create safer work environments, enhance compliance, and protect their most valuable asset—their workforce.
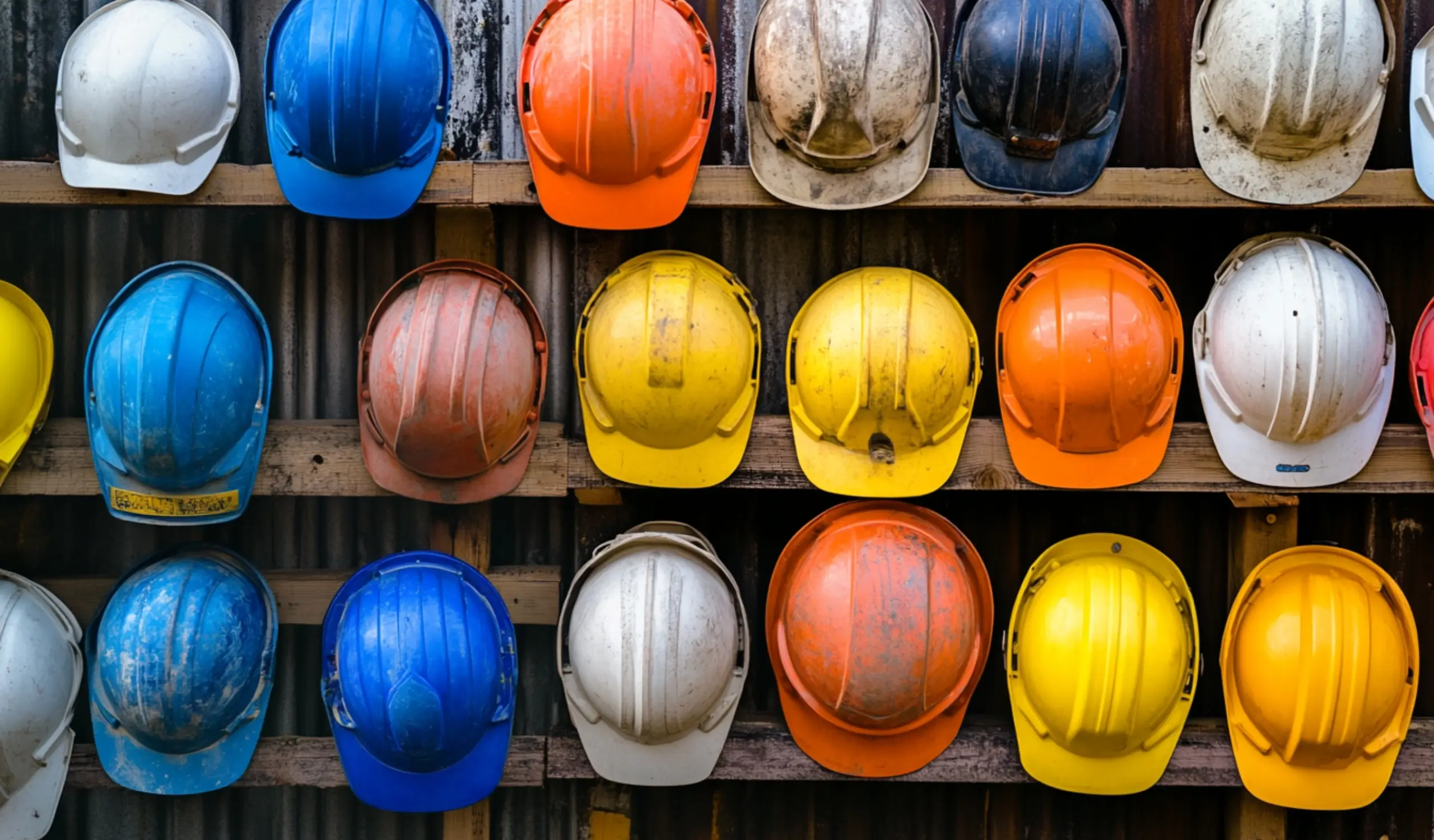
Global Standards and Regulations in Occupational Safety And Health (OSH)
Global standards and regulations in Occupational Safety And Health (OSH) provide frameworks for creating safe and healthy workplaces. These guidelines are essential for maintaining consistent safety practices across industries and regions, ensuring workers’ well-being, and fostering productivity. Below is a detailed exploration of some of the key global OSH standards and regulations:
1. ISO 45001: Occupational Safety And Health Management Systems
ISO 45001 is an internationally recognized Occupational Safety And Health Management Systems (OHSMS) standard. It provides a structured framework for managing workplace risks and improving safety performance.
Key Features:
- Risk-Based Approach: Focuses on identifying and mitigating potential hazards before they lead to incidents.
- Employee Involvement: Encourages worker participation in developing and implementing safety measures.
- Continuous Improvement: Promotes ongoing evaluation and enhancement of safety systems.
- Compatibility with Other Standards: Aligns with ISO 9001 (Quality Management) and ISO 14001 (Environmental Management) for integrated systems.
Benefits:
- Ensures compliance with legal requirements.
- Enhances safety culture across the organization.
- Reduces workplace accidents and associated costs.
2. OSHA (Occupational Safety and Health Administration)
OSHA is a U.S.-based regulatory body under the Department of Labor that sets and enforces workplace safety standards.
Key Provisions:
- General Duty Clause: Employers must provide a workplace free from recognized hazards.
- Industry-Specific Standards: OSHA provides tailored regulations for construction, healthcare, and manufacturing industries.
- Employee Rights: Workers have the right to a safe workplace, access to safety information, and the ability to report violations without retaliation.
Impact:
- OSHA has significantly reduced workplace fatalities and injuries in the United States since its establishment in 1971.
- It offers valuable resources, training, and consultation services to employers.
3. ILO (International Labour Organization) Guidelines
The International Labour Organization (ILO), a United Nations agency, sets global standards for labor practices, including OSH.
Key Guidelines:
- Convention 155: Focuses on OSH and the working environment, emphasizing national policies to prevent workplace accidents.
- Convention 161: Establishes the role of occupational health services in monitoring and promoting workplace safety.
- Code of Practice: Offers practical recommendations for managing risks in specific sectors, such as mining or chemicals.
Benefits:
- Promotes universal principles of safe and healthy work environments.
- Encourages countries to adopt comprehensive OSH policies and laws.
- Addresses emerging issues like psychosocial risks and digitalization.
4. European Union (EU) OSH Directives
The EU has implemented a series of directives to harmonize workplace safety standards across its member states.
Key Directives:
- Framework Directive 89/391/EEC: Establishes the basic principles for workplace safety and health, requiring employers to assess risks and implement preventive measures.
- Sector-Specific Directives: Cover industries such as construction, chemicals, and transport.
- Worker Participation: Emphasizes involving employees in OSH decision-making processes.
Impact:
- Encourages uniform safety practices across EU countries.
- Protects millions of workers within the European Economic Area.
5. National Standards
Each country has its own OSH laws and regulations, often influenced by global standards.
Examples:
- Canada: Occupational Safety And Health regulations are managed at both federal and provincial levels, with agencies like WorkSafeBC.
- Australia: Safe Work Australia develops national policies and monitors compliance with OSH standards.
- India: The Occupational Safety, Health, and Working Conditions Code, 2020, consolidates laws related to worker safety.
Key Focus Areas:
- Adapting global best practices to local contexts.
- Ensuring compliance with industry-specific requirements.
- Addressing unique hazards present in specific regions.
6. Industry-Specific OSH Standards
Certain industries have additional regulations due to the unique risks they pose.
Examples:
- Construction: Standards focus on fall protection, scaffolding, and equipment safety.
- Healthcare: Regulations address biological hazards, patient handling, and workplace violence.
- Oil and Gas: Emphasizes process safety management and emergency preparedness.
7. Emerging Focus: Psychological Safety
Global OSH standards increasingly emphasize mental health and psychosocial risks, such as stress, bullying, and burnout.
Key Developments:
- ISO 45003: A guideline for managing psychological health in the workplace, complementing ISO 45001.
- ILO Initiatives: Promote awareness of mental health issues in labor policies.
Challenges in Implementing Global Standards
- Cultural Differences: Safety practices may vary based on cultural norms and work attitudes.
- Resource Constraints: Small and medium-sized enterprises (SMEs) often face challenges in implementing comprehensive OSH systems.
- Evolving Risks: Rapid technological advancements and climate change introduce new workplace hazards.
Global standards and regulations in OSH provide essential frameworks for ensuring safe workplaces worldwide. By adopting these guidelines, organizations can protect employees, enhance productivity, and comply with legal obligations. Whether through ISO 45001, OSHA regulations, or ILO conventions, a commitment to these standards is vital for creating a safety culture in every workplace.
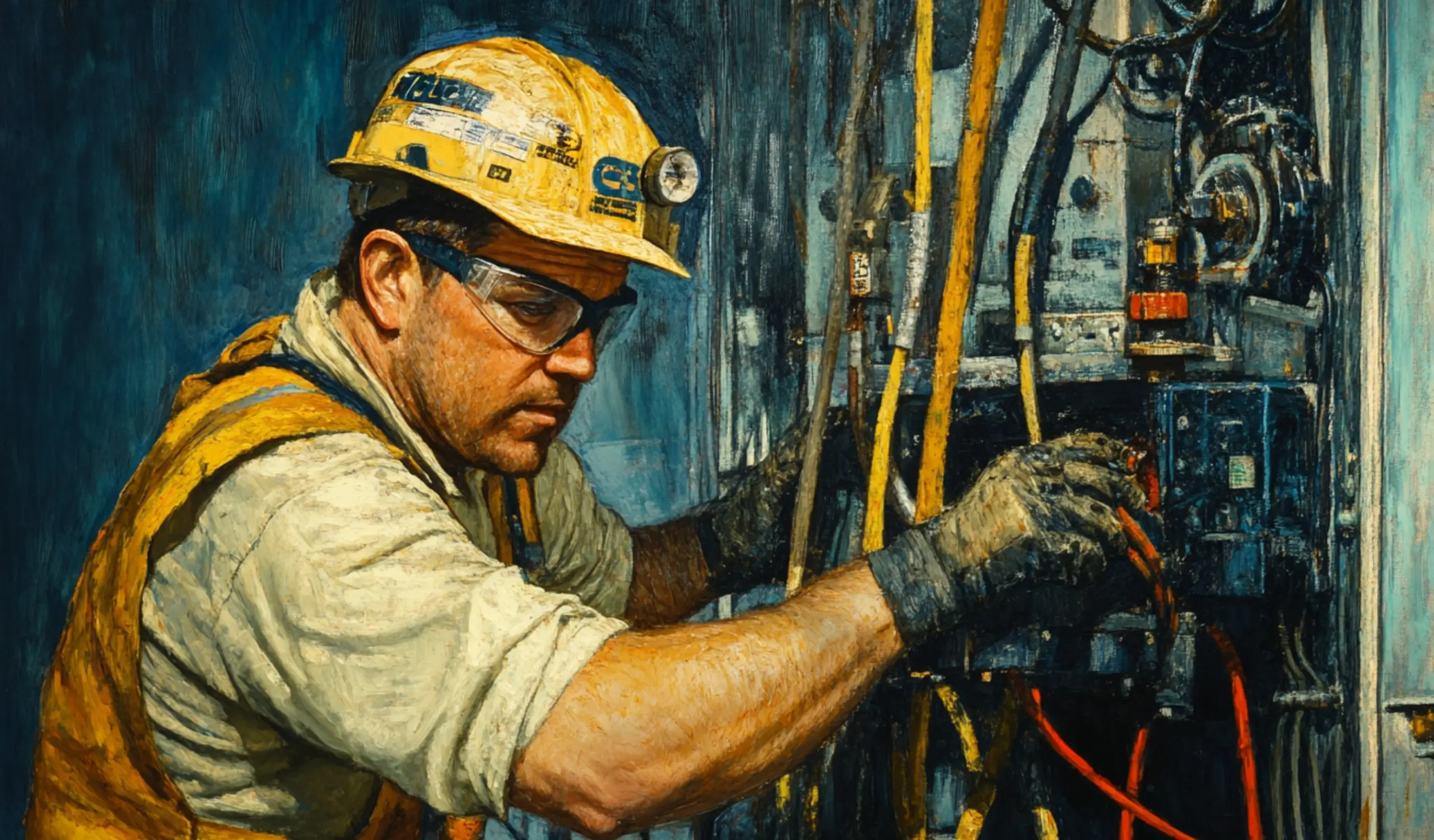
How to Build a Strong OSH Culture
Building a strong Occupational Safety And Health (OSH) culture requires commitment, collaboration, and consistent effort across all levels of an organization. A robust OSH culture ensures that safety becomes a core value, not just a regulatory requirement, and promotes proactive behaviors that reduce workplace risks.
Here’s a comprehensive guide to developing and maintaining a strong OSH culture:
1. Leadership Commitment
Leadership plays a pivotal role in shaping an organization’s approach to safety. When leaders prioritize OSH, it sets the tone for the entire organization.
- Demonstrate Accountability: Leaders should model safe behaviors and visibly support OSH initiatives.
- Allocate Resources: Invest in training, equipment, and systems that enhance workplace safety.
- Set Clear Expectations: Define safety objectives and ensure they are communicated effectively.
- Participate Actively: Attend safety meetings, inspections, and training sessions to reinforce their importance.
2. Employee Involvement
Employees are the backbone of a strong OSH culture. Engaging them in safety efforts fosters a sense of ownership and collective responsibility.
- Encourage Reporting: Establish an open-door policy where employees feel safe reporting hazards or incidents without fear of retaliation.
- Create Safety Committees: Involve workers from different departments to provide diverse perspectives on safety issues.
- Recognize Contributions: Reward employees who demonstrate commitment to safety or suggest innovative improvements.
3. Comprehensive Training and Education
Education empowers employees to recognize, avoid, and respond to hazards effectively.
- Onboarding Programs: Ensure new hires understand workplace safety policies and procedures.
- Ongoing Training: Offer refresher courses and specialized training for roles with unique risks.
- Practical Drills: Conduct regular emergency simulations, such as fire drills or spill containment exercises.
- Tailored Content: Customize training for diverse roles and learning styles, including multilingual materials if needed.
4. Clear Communication
Effective communication ensures everyone understands the organization’s safety expectations and initiatives.
- Regular Updates: Share information about new safety policies, procedures, and achievements through emails, meetings, or noticeboards.
- Feedback Channels: Allow employees to share concerns or suggestions for improving safety measures.
- Simplified Messaging: Use clear, concise language and visual aids to make safety information accessible to all.
5. Recognition and Rewards
Acknowledging efforts to maintain safety boosts morale and reinforces positive behaviors.
- Safety Milestones: Celebrate achievements, such as accident-free days or successful audits.
- Incentive Programs: Offer rewards for exemplary adherence to safety protocols or innovative solutions.
- Team Recognition: Highlight collective achievements to foster teamwork and mutual accountability.
6. Establish Clear Policies and Procedures
Safety policies and procedures form the foundation of an OSH culture. These guidelines should be well-documented, easily accessible, and regularly updated.
- Comprehensive Manuals: Outline the organization’s safety objectives, protocols, and emergency procedures.
- Defined Roles: Clearly specify responsibilities for safety at every level of the organization.
- Policy Reviews: Regularly evaluate and update policies to address emerging risks or regulation changes.
7. Foster a Proactive Approach
A proactive safety culture focuses on preventing incidents rather than reacting to them.
- Hazard Identification: Regularly inspect the workplace for potential risks and address them immediately.
- Risk Assessments: Evaluate tasks and equipment to identify and mitigate hazards.
- Incident Investigations: Analyze near-misses and accidents to uncover root causes and implement corrective actions.
8. Utilize Technology and Innovation
Leveraging modern tools and technologies can streamline safety management and improve outcomes.
- Wearable Devices: Monitor employees’ health and alert them to potential hazards in real-time.
- Safety Apps: Use digital platforms for incident reporting, training, and communication.
- Predictive Analytics: Identify patterns and predict potential risks using data from past incidents.
9. Build a Culture of Continuous Improvement
A strong OSH culture is not static; it evolves with changing workplace dynamics and advancements.
- Regular Audits: Conduct internal and external audits to assess the effectiveness of safety measures.
- Stay Informed: Keep up with industry trends, emerging risks, and regulatory changes.
- Employee Feedback: Use surveys and discussions to gather insights on improving safety practices.
10. Promote Psychological Safety
In addition to physical safety, fostering mental well-being is a critical aspect of a strong OSH culture.
- Support Systems: Provide access to mental health resources, such as counseling services or employee assistance programs.
- Reduce Stressors: Manage workloads and deadlines to minimize stress and prevent burnout.
- Inclusive Environment: Create a respectful and supportive workplace where employees feel valued.
11. Align Safety with Organizational Goals
Integrate OSH into the company’s mission and values to emphasize its importance.
- Strategic Integration: Include safety metrics in organizational performance reviews.
- Cross-Functional Collaboration: Ensure all departments understand their role in maintaining safety.
- Public Commitment: Share the organization’s dedication to safety with stakeholders, clients, and the community.
12. Regularly Measure and Share Progress
Tracking and communicating safety progress keeps everyone informed and motivated.
- Performance Metrics: Monitor key indicators, such as injury rates, near-misses, and training completion rates.
- Transparent Reporting: Share results with employees and stakeholders to maintain accountability.
- Celebrate Improvements: Highlight progress to reinforce the value of safety efforts.
Building a strong OSH culture requires unwavering leadership, employee engagement, and a commitment to continuous improvement. By prioritizing safety as a core value, organizations can create a work environment where employees thrive, risks are minimized, and productivity soars. Investing in a robust OSH culture safeguards lives and strengthens the foundation for long-term success.
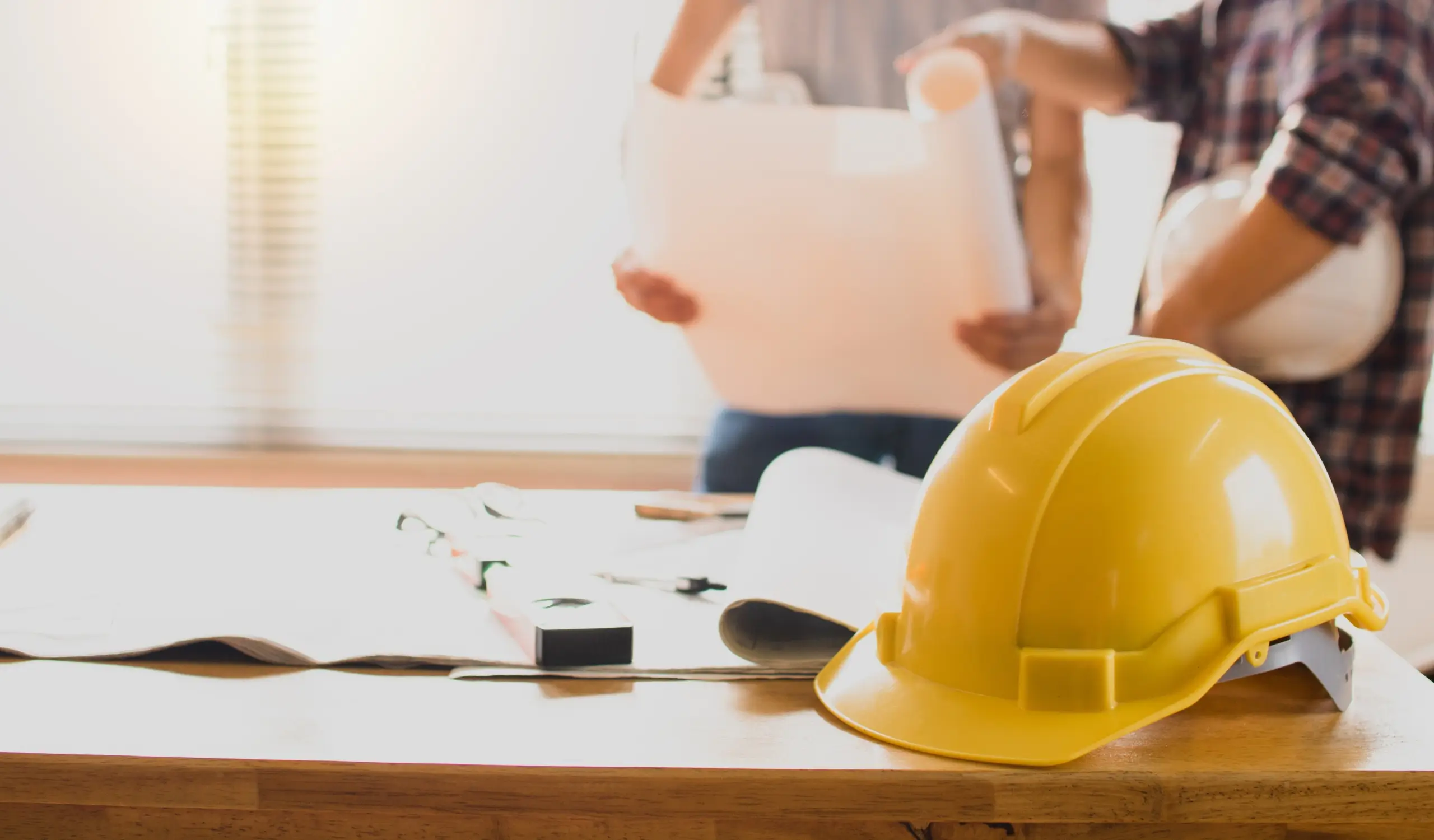
Technological Innovations in OSH
Technological advancements have significantly transformed the landscape of Occupational Safety And Health (OSH), enabling organizations to identify, mitigate, and manage workplace risks more efficiently. These innovations not only enhance safety practices but also streamline compliance, improve monitoring, and empower employees to work in safer environments.
Below is an exploration of key technological innovations revolutionizing OSH:
1. Wearable Technology
Wearable devices play a pivotal role in real-time health monitoring and hazard detection, offering workers and organizations a proactive approach to safety.
Applications:
- Health Monitoring: Devices like smartwatches and fitness trackers monitor heart rate, fatigue, and stress levels to prevent overexertion.
- Environmental Alerts: Smart helmets and vests detect hazardous conditions such as high temperatures, harmful gases, or excessive noise levels.
- Fall Detection: Sensors in wearable gear can identify falls or slips and send alerts to emergency responders.
Benefits:
- Immediate detection of unsafe conditions.
- Reduction in workplace accidents through early warnings.
- Enhanced data collection for analyzing trends and improving safety protocols.
2. Internet of Things (IoT)
IoT enables interconnected devices to collect, analyze, and share data, providing organizations with valuable insights into workplace safety.
Applications:
- Smart Sensors: Detect gas leaks, fire hazards, or unsafe machinery operations and send real-time alerts.
- Connected Workplaces: Track equipment usage, worker location, and environmental conditions through a centralized system.
- Predictive Maintenance: IoT sensors identify equipment wear and tear, preventing breakdowns and accidents.
Benefits:
- Improved hazard detection and faster response times.
- Efficient resource management and reduced downtime.
- Comprehensive data for predictive analytics.
3. Artificial Intelligence (AI) and Machine Learning
AI and machine learning are transforming OSH by analyzing vast amounts of data to predict and prevent potential risks.
Applications:
- Predictive Analytics: Analyze historical data to identify patterns and predict future incidents.
- Risk Assessment: Use AI to evaluate job sites and recommend tailored safety measures.
- Behavior Analysis: Monitor employee actions to detect unsafe behaviors and provide corrective guidance.
Benefits:
- Data-driven decision-making.
- Reduced human error in risk assessments.
- Continuous improvement through automated insights.
4. Virtual Reality (VR) and Augmented Reality (AR)
VR and AR are revolutionizing training and hazard simulations, offering immersive and interactive learning experiences.
Applications:
- Virtual Training: Simulate real-life scenarios, such as fire drills, machinery operations, or hazardous material handling, in a controlled environment.
- AR Tools: Overlay digital instructions or hazard warnings in real-world environments using AR glasses or devices.
- Emergency Preparedness: Train employees to respond to emergencies without exposing them to actual risks.
Benefits:
- Enhanced retention of safety training.
- Risk-free practice of high-stakes tasks.
- Improved engagement and comprehension.
5. Robotics and Automation
Automation reduces human involvement in dangerous tasks, minimizing exposure to risks.
Applications:
- Dangerous Tasks: Robots handle hazardous processes, such as handling toxic chemicals or operating in extreme environments.
- Inspection and Maintenance: Automated drones and robots inspect high-risk areas like confined spaces or elevated structures.
- Workplace Assistance: Collaborative robots (cobots) assist workers in physically demanding tasks.
Benefits:
- Reduced workplace injuries in high-risk tasks.
- Increased efficiency and precision.
- Lower long-term costs associated with injuries and insurance.
6. Mobile Safety Applications
Mobile apps simplify safety management, allowing employees and managers to access critical information on the go.
Applications:
- Incident Reporting: Employees can report hazards or near-misses directly through mobile platforms.
- Safety Checklists: Digital checklists ensure compliance with safety protocols during inspections or daily tasks.
- Training Modules: Mobile-friendly training resources enable employees to learn at their convenience.
Benefits:
- Streamlined communication and reporting.
- Increased accessibility to safety tools and training.
- Enhanced compliance tracking.
7. Big Data and Analytics
Big data provides a wealth of information for understanding and improving OSH practices.
Applications:
- Trend Analysis: Identify patterns in workplace incidents to develop targeted prevention strategies.
- Safety Scorecards: Use data to evaluate and compare safety performance across departments or locations.
- Compliance Monitoring: Track adherence to regulations using data dashboards.
Benefits:
- Informed decision-making.
- Continuous improvement of safety measures.
- Better resource allocation for addressing high-risk areas.
8. Drones
Drones are increasingly being used for monitoring, inspection, and emergency response.
Applications:
- Aerial Inspections: Inspect hard-to-reach areas like roofs, pipelines, or construction sites.
- Emergency Response: Survey disaster-affected areas to identify hazards and prioritize rescue operations.
- Environmental Monitoring: Track air quality, temperature, or other environmental factors in large workspaces.
Benefits:
- Reduced need for workers to enter hazardous zones.
- Faster and more comprehensive inspections.
- Cost-effective solutions for large-scale monitoring.
9. Blockchain for Safety Records
Blockchain technology ensures secure and transparent record-keeping for safety compliance.
Applications:
- Incident Logs: Maintain tamper-proof records of workplace incidents and inspections.
- Certification Verification: Store training certifications securely to verify employee qualifications.
- Regulatory Compliance: Use blockchain for transparent reporting to regulators and stakeholders.
Benefits:
- Enhanced trust and accountability.
- Simplified auditing processes.
- Secure and accessible safety data management.
10. Gamification in Safety Training
Gamification integrates game-like elements into safety training, making learning engaging and impactful.
Applications:
- Interactive Quizzes: Employees earn points or badges for completing safety quizzes.
- Simulated Challenges: Use game scenarios to teach hazard recognition or emergency response.
- Leaderboards: Encourage friendly competition to motivate employees to excel in safety practices.
Benefits:
- Increased employee engagement in training.
- Better retention of safety knowledge.
- Encourages proactive participation in safety initiatives.
Challenges in Implementing OSH Technology
While technological innovations offer tremendous benefits, organizations may face challenges such as:
- Cost Constraints: High upfront investment for advanced technologies.
- Training Requirements: Employees need to be trained to use new tools effectively.
- Data Security: Managing sensitive data from wearable devices and IoT systems requires robust cybersecurity measures.
Technological innovations in OSH are revolutionizing workplace safety, making it more proactive, efficient, and effective. By leveraging tools like wearables, IoT, AI, and VR, organizations can ensure compliance and create a safer and more productive environment for employees. Embracing these technologies is no longer optional—it’s a necessity for businesses committed to protecting their workforce and achieving long-term success.
Conclusion: Making OSH a Priority
Occupational Safety And Health is more than a legal requirement—it’s a cornerstone of ethical business practices and sustainable growth. By prioritizing OSH, organizations can protect their workforce, enhance productivity, and establish themselves as leaders in their industries.
Key Takeaways:
- OSH is essential for the health, safety, and well-being of employees.
- Effective programs include hazard identification, employee training, and continuous monitoring.
- Compliance with global standards and leveraging technology can improve workplace safety.
Remember, a safe workplace is a productive one. By embedding OSH into your organizational culture, you ensure the safety of your team and the success of your business.